スペシャライズドは、ミラーテクノロジーを使用して作成された新しいパワーサドルを発表。
このテクノロジーでは、デジタルライト合成と呼ばれるプロセスを使用して、液体ポリマーからサドルを3Dプリントして作られる。
Specializedは、独自のCLIP(Continuous Liquid Interface Production)テクノロジーを使用する会社であるCarbonと3D印刷製品のパートナーシップを締結して、全く新しい製造方法のサドルを開発した。
S-Works Power Saddle with Mirror Technology
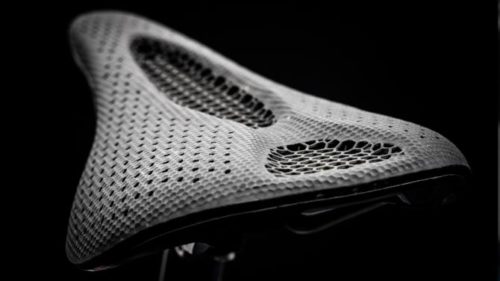
Photo Specialized.com
S-Works Power Saddleは、内部のハニカム構造を使用して、快適性と圧力分布の点でパフォーマンスを改善。
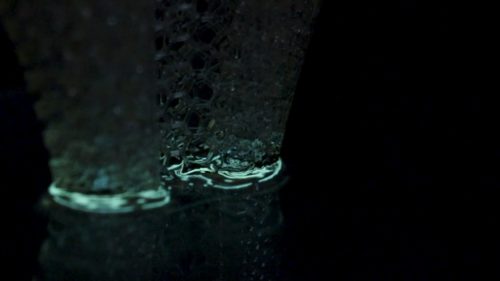
S-Works Power Saddleの3Dプリント制作
化学反応が起こる前に、光を使用してハニカム構造を3D印刷し、材料の最終特性を強化および設定する。
この構造は、サドルの従来のクッションに代わるものでカーボンベースに固定される。
つまり、従来のサドルの作成方法とは全く違う製造方法となっている。
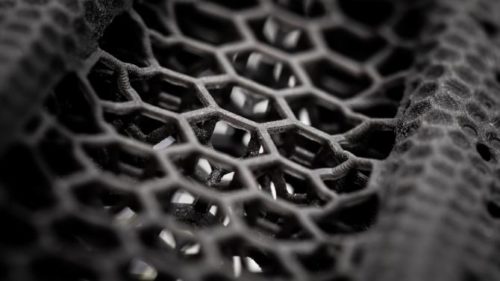
サドル中央付近のハニカム構造
14,000個のストラットと、7,799個のノードで構成される特許出願中のハニカム構造で構成されており、それぞれを個別に調整して、ポリマー密度を無限に変えることが出来る。
つまり、各個人に合わせて作成することが可能という訳だ。
3Dプリントなので、作成にかかる時間は従来よりも格段に速くなる。
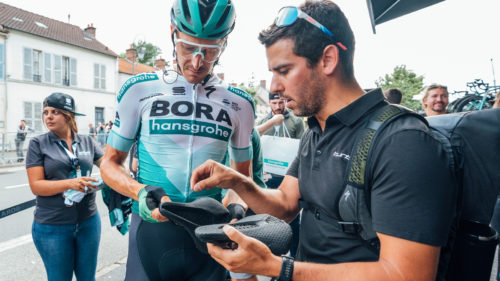
Marcus Burghardtがサドルをチェック
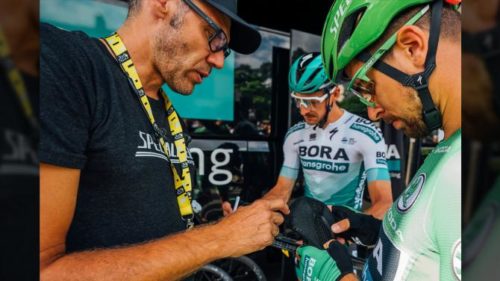
サガンはツール・ド・フランスで初めてサドルを見る
サドルは、Bora-Hansgroheと、Deceininck-Quickstepのライダーによってすでにテストされている。
、
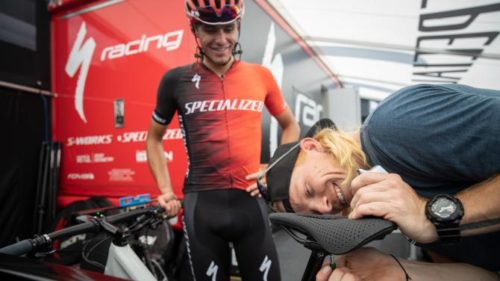
Christopher Blevinsは、Val di Doleのレースで使用
ロードだけでなく、MTBのレースでもテスト。
Val di Sole UCI MTBワールドカップ中にChristopher Blevinsによって実際にレースで使用された。
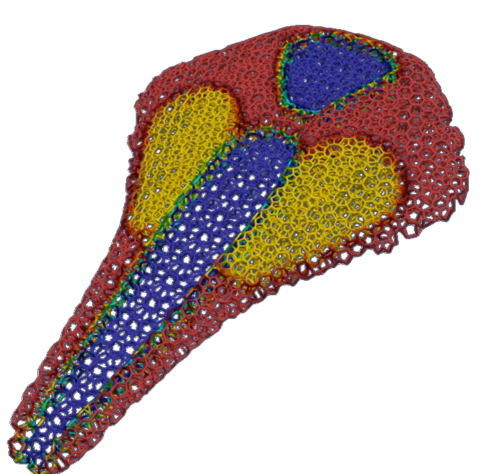
ミラーテクノロジーの圧力マッピング
SpecializedのBody Geometryチームは、男性と女性の両方でミラーテクノロジーが軟部組織の圧力を下げ、陰茎の血流を確保し、座り心地を改善しているか検証した。
この新技術は、製造時間だけでなく研究開発もスピードアップできる。
S-Worksサドルの最終設計に到達する前に、SpecializedとCarbonは10か月にわたって70の異なるサドルを作製。
これは、通常、新しい自転車のシートを製造するのにかかる開発時間の約半分となる。
SpecializedとCarbonはは、この技術に大きな期待を寄せている。
すでに振動減衰と骨盤の安定性の改善のためにテクノロジーをテストしており、ライダーが個々の好みに基づいてカスタム印刷されたタッチポイントを持つことができる未来を想定している。
Specializedは、S-Works Power Saddleの小売価格をまだリリースしておらず、いつ市販されるかについての発表もない。
だが、レビューサンプルは、2020年初頭にプレスするために会社から納品される予定となっている。
サドルは143mmと155mmの2つの幅で入手できるようになる予定。
ついに、サドルの世界にも3Dプリントの技術が入ってきましたね。
サドルによる痛みは各個人によって違うので、人それぞれの要望にあったサドルが手にはいるようになればより快適になりそうです。
コメント