現在のフレーム形状では、トラスで組まれたフレームは発展していない。
過去に、トラス構造のフレームは発表されているけれど、大きく進歩しているということはない。
トラスとは、部材を3角形に組んだ形のことだけど、フレームの断面でトラスを使うことがないのは何故だろうか?
トラス断面のフレーム

photo delta7bikes
上記のように2013年にDelta 7がトラス形状のフレームを発表。
特許取得済みのオープンラティス、スパイダーウェブバイクデザインは、適切な補強間隔で材料を濃縮し、余分な材料を排除することにより、IsoTrussカーボンファイバーの強度からより高い効率を持っている。
気になる重量だけど、フレーム重量は860g。中空になっているのだから、もっと軽くても良さそうだけど、2013年に作られたならば物凄く軽い。
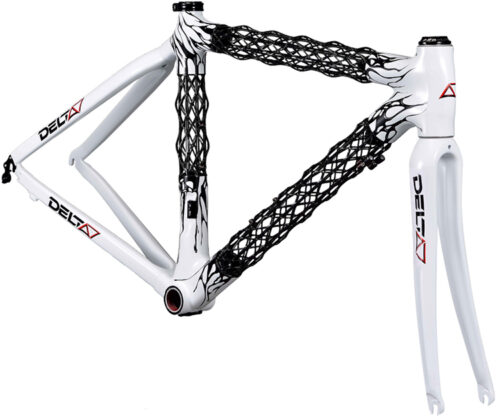
photo delta7bikes
フレームは16本作られ9本が販売済み。強度はかなり高い。それは以下の動画で見てもわかる。
それは、簡単に言うと対費用効果の点で問題があるからだ。
トラスセクションは複雑な製造を必要とする。各セクションは個別に作成され、他のフレームコンポーネントと手動で統合される。このプロセスは時間がかかり、費用がかかるということだ。
しかも、手動なので大量生産に向かない。今ならば、3Dプリントがあるので、違うかもしれないけど。
Delta 7のフレームがいくらで販売されたのかは、公式サイトにも情報がない。
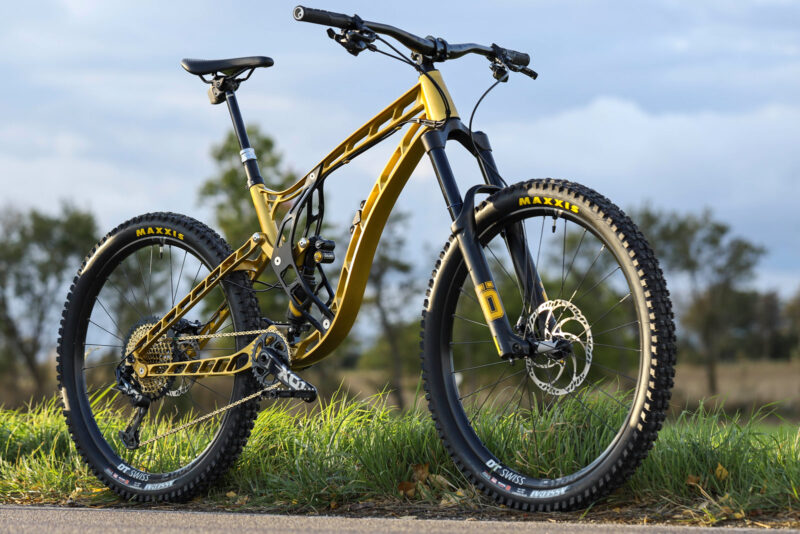
Frace F160は、70kgのアルミニウムスラブから機械加工 photo frace
トラス構造のフレームは、検索すると何台かはヒットする。形としては面白いのだけど、コストがかかるので、発展することはないでしょうね。
すでに、カーボンフレームで600g台の重量で作成することが出来るので、わざわざコストをかけて作る必要がないというのが結論のようだ。
コメント